Blog
Written By: Satya Jayadev, Sunil Kumar, Pavithra
From the bustling automotive plants to the intricate pharmaceutical industries, Indian manufacturing stands at a transformative crossroads, a pivotal sector for the nation’s economic growth and sustainability. However, the sector faces significant challenges that can minimize their global presence. Fluctuating raw material costs, maintaining consistent product quality, optimizing production processes, and minimizing waste are just a few of the hurdles that manufacturers must overcome. This blog explores the role of blend optimization solutions like OptiBlend, and the prowess of data analytics innovations in ensuring a competitive edge in the global market.
With globalization intensifying competition, the manufacturing industry faces several critical challenges that can impact its performance and sustainability:
- Ensuring consistent product quality is vital for customer satisfaction and regulatory compliance. Variations in raw materials and manual processes can lead to inconsistencies, damaging brand reputation and causing financial losses.
- The volatility of raw material prices impacts profitability. Manufacturers must optimize material use to stay cost-effective without compromising quality.
- Relying on manual adjustments and trial-and-error methods is time-consuming and error-prone, leading to inefficiencies and increased production costs.
- Outdated technologies limit competitiveness on a global scale. Integrating advanced tools is necessary for modernization and improved operational efficiency.
OptiBlend, an AI based tool that optimizes blending processes through automated data-driven modelling. It provides innovative solutions to tackle the above challenges for precision proportions and consistent quality, by:
- Enabling configuration of the variables involved in any blend process through an intuitive user interface, with ease.
- Generating AI driven models to capture suitable data-based relations between the blend variables by feeding data pertaining to raw materials, their properties, blending parameters and output product properties. Known or customised models can also be incorporated into the application.
- Using the generated models to predict values of unknown output properties for given inputs.
- Optimizing various aspects of the blend process such as cost, quality, yield, wastage, etc. while ensuring that the blend output properties remain in desired range, through a simple interface.
- Leveraging existing models and inbuilt solvers to compute the control parameters while optimizing the objective.
OptiBlend ensures reduced production costs , improved product quality, and minimized waste by leveraging advanced AI tools and solvers for blending processes. Its applications span diverse industries, demonstrating effectiveness in addressing industry-specific blending challenges. Some significant implemented use cases include:
Sand foundries: The goal was to optimize raw material ratios in sand mixing to reduce costs. By leveraging data-driven models, OptiBlend identified the optimal blend of new sand, return sand, coal dust, water, bentonite, and inert fines. This approach led to up to 20% cost savings in raw material usage for the daily mixing of 1000 tons of sand. Also, using blend models to predict output properties and rejection rates, resulted in a 5% reduction in rejection rates, enhancing product quality while reducing costs.
Olive Oil Blending: Achieving cost efficiency while maintaining high-quality standards is crucial. By utilizing advanced data-driven models, OptiBlend determined the optimal proportions of each olive oil variety, ensuring the desired flavor, aroma, and quality at significantly reduced production costs. The outcome was a remarkable achievement of up to 10% cost savings, highlighting optimization effectiveness and enhanced efficiency, without compromising the quality of the olive oil blend.
Some more use cases in various industries:
Pharmaceuticals: Dosage accuracy and stability, homogeneity and compressibility in powder blends, by optimizing the mix of active ingredients and excipients.
Chemicals: Optimize pigment and resin blends for consistent color and durability, enhanced viscosity and drying time by adjusting polymer and filler ratios.
Petroleum: Improved combustion efficiency and reduce emissions by optimizing hydrocarbon and additive blends. Enhanced lubricity and thermal stability through optimal base oil and additive combinations.
Construction: Enhanced compressive strength and consistency in cement mixes, optimized ingredient proportions in concrete for improved strength and setting time. Increased load-bearing capacity and durability of asphalt mixes.
Embracing innovation and technology is essential for growth, and the manufacturing industry is no exception. As the industry evolves, tools like OptiBlend will play a pivotal role in shaping the future of manufacturing. By offering advanced blending and optimization solutions, OptiBlend addresses the key challenges faced by manufacturers, ensuring improved efficiency, quality, and sustainability.
Ensure your manufacturing processes are ready for the future. Connect with us to see how OptiBlend can work for you. https://systechusa.com/optiblend
Related Resources:
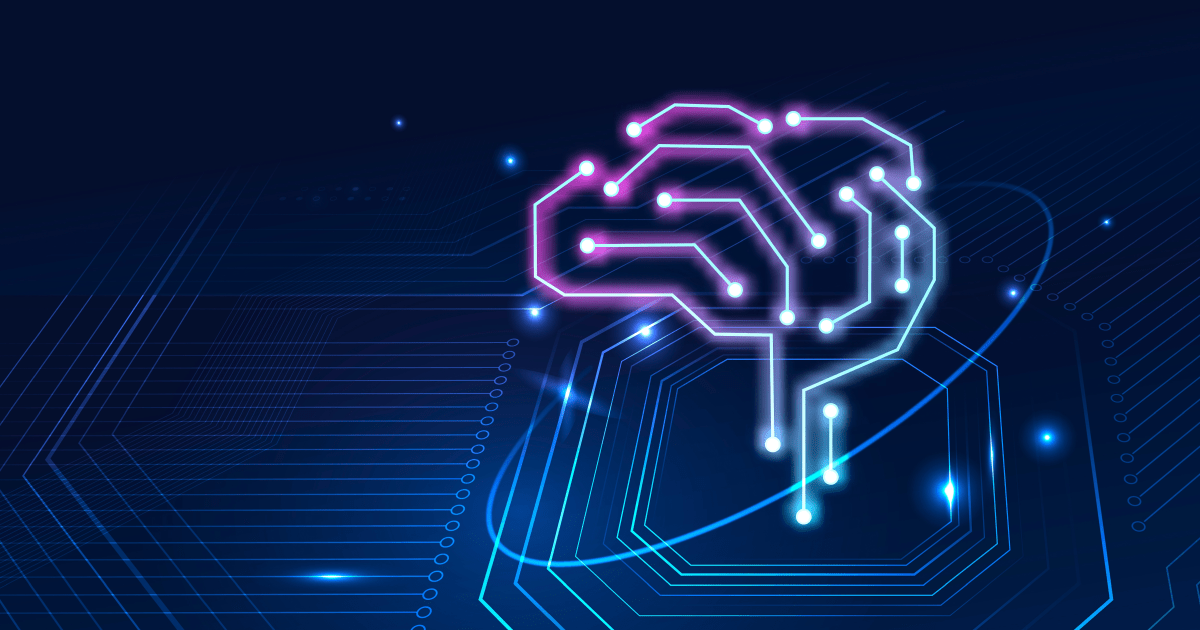
AI and ML Solutions
Automate, enrich, and innovate with Systech’s comprehensive Data Science, ML, and GenAI service offerings.
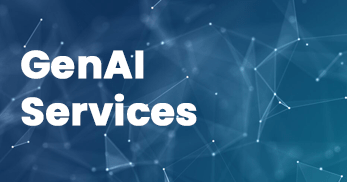
Harness the Power of Generative AI
At Systech, we’re at the forefront of integrating Generative AI (GenAI) into our services and solutions, revolutionizing how businesses leverage their data.
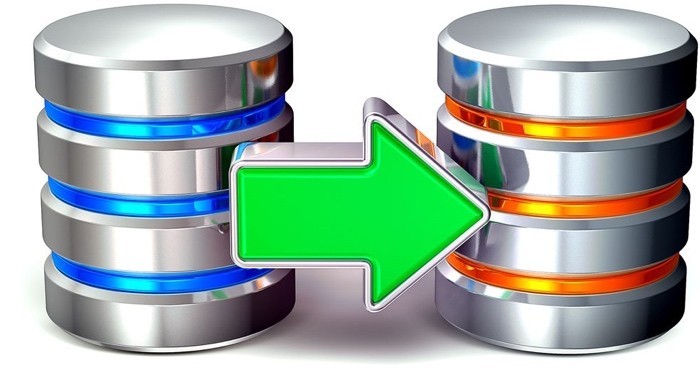
DBShift™ – Modernization Accelerator
Our flagship utility app, DBShift™ enables smooth and error-free migration to Cloud.